Getting Started
Getting started with a new system can be easier than you think. Check out our articles about how systems are implemented in practice.
We have seen a lot of ERP implementations. Don’t hesitate to contact us to discuss how we can get your company to the next level of automated business processes.
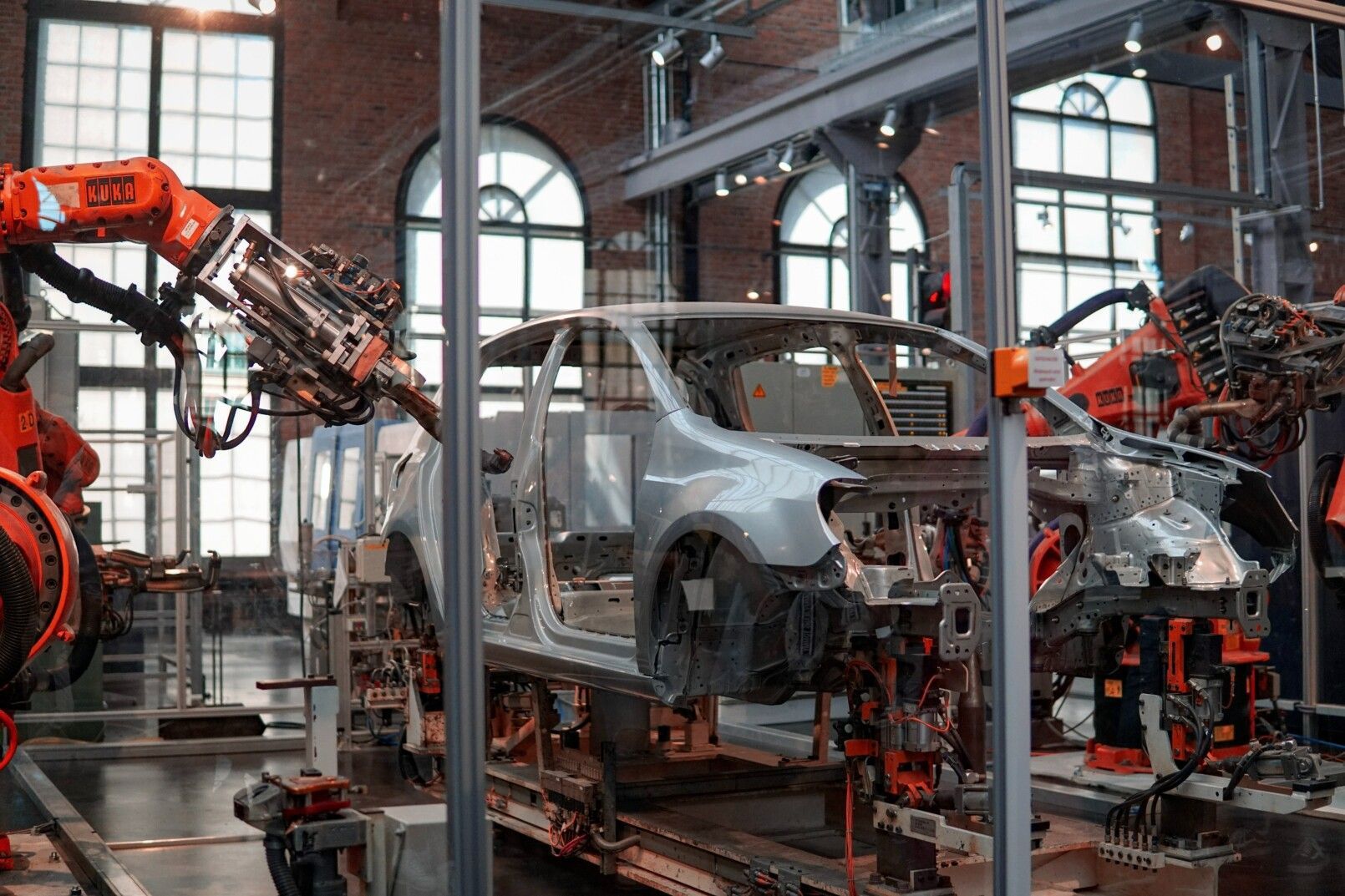
Three things to begin with that we think are critical for a successful implementation of your new ERP system. 1. How clean is your data? If you are getting good data from a previous system, then fine. If not then think how are you going to get clean data to start with your system. There are three main kinds of data: Customers and suppliers a.k.a. Contacts or Partners Items a.k.a. SKU’s or materials Product structures a.k.a Bills of Materials. Usually the last is the most difficult to get. But you normally need it to do manufacturing. (The exception is if you are a job shop where each job is different). Each of them can be pre-prepared in an Excel spreadsheet. If you can’t get these, there is another possibility: start using an empty system and create the data each time an order comes in. You sales admin will probably strangle you after a few months, but this is possible. 2. Verify that the system suits your requirements. The great thing about nearly any cloud product is the trial period. Use it. Set up your basic business process (or processes) and run trial orders through the system with at least a sample of good real data. Accountancy system are reasonably the same all the world over (they’re all debits and credits, right?) and are set by tax authorities. ERP, especially in manufacturing, is not. Everyone has an opinion of how it works. Don’t decide on a go live date, go live and then start wondering why some treasured business feature (that of course you had in your previous customised system) is missing. In particular look carefully at the few reports that you consider critical for your business. Compare them with any reports that you have in your legacy system, so that when you go live your users do not immediately complain that they can not get the information that they used to get. This can be due to data migration issues or report design. Both of these can be resolved, but normally it will take at least a few days to go back for instance redo the data migration or order custom reports. Check all the hardware and network equipment is what you need. If you are using barcode label printers make sure these are coded and tested with Manu Online. DO NOT GO LIVE UNTIL YOU CAN RUN TRIAL ORDERS THROUGH ALL ASPECTS OF YOUR PROCESS IN DETAIL. You will punish yourself and your team if you assume that every detail of our manufacturing ERP system works in the same way as the previous one that you used. 3. Get training Get training from Manu Online or a partner. We see that our system is found easy to use if you have good experience with any medium-sized legacy ERP system. If you are not familiar with ERP, then you will find it hard to go. Two or three training sessions with one of our consultants will take you a long way in getting your system running effectively. More information accessed here .