Production
Production
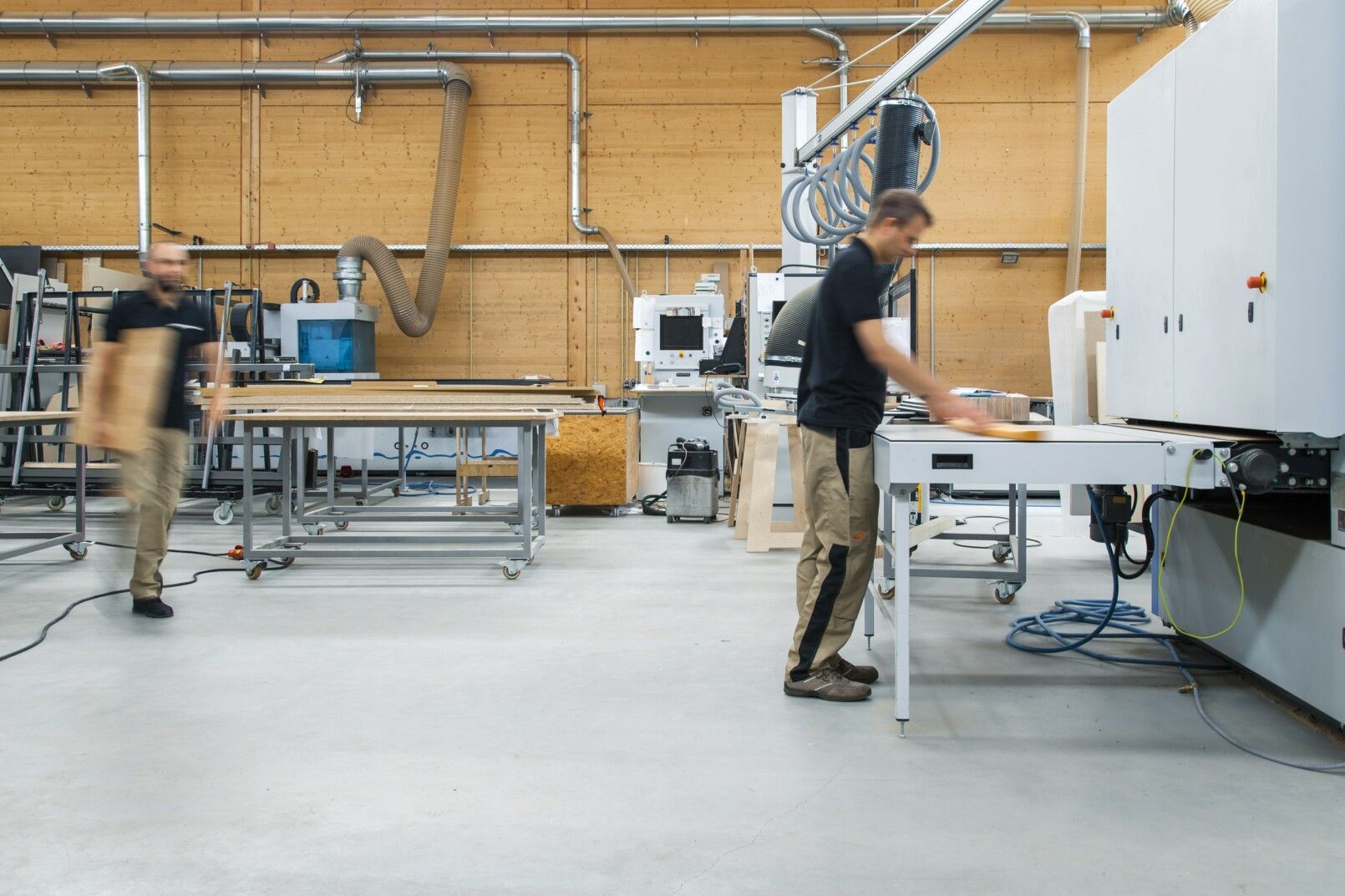
Production work orders
When creating a new work order, the user is prompted to select from planned operation elements from the planning system. Each of these operation elements is created by a sales order or by a work order of a product higher in the production process. Each element is based on the operation template for the manufactured item. In this way it is possible to closely tie work orders to customer sales orders. If the work order quantity is greater than the total for all the elements, then the remaining quantity in the work order is unallocated. This unallocated quantity may be allocated by the resource planning system automatically at any time that the work order is open.
When creating a new work order, the user may specify that the whole work order is to be carried out at a subcontractor. Then users whose user id is associated with a certain subcontractor have the ability to access the work order and carry out the required procedures.
Having selected the appropriate elements and specified the quantity, the user can request a work order number.
The work order is created with the default route from the operation template. The user may now edit this route, for instance to balance load between different work cells or to change part of the work to a subcontractor.
If the work order is routed, data entry can be managed at the individual cells by opening the system by cell rather than work order. When viewing work orders by cell it is also possible to see the status of queuing at each cell.
As with all the operations, the final stage is ‘Mark as complete’. This will ensure that all data entry activities are complete and close the work order.
Create multiple work orders
The make to stock work order has a special feature to enable the user to create multiple work orders based on the planned requirements as calculated by the system. Thus even in complex and large volume manufacturing it is possible to create work orders very easily.
The two basic planning features are based on demand and on minimum stock level. Demand is calculated from sales order demand and for subassemblies, the creation of work orders for parent products whether needed for sales orders or not. Minimum stock level is based on minimum free stock level. The system will create new work orders even if the product is in stock, but the free stock level has fallen below the minimum specified amount.
An interesting feature when creating multiple work orders is the property “maximum batch size”. For instance if this is set to 1, then the system will create 5 separate work orders if 5 items are required. In this way Manu Online can be set up to support the “batch size of 1” manufacturing philosophy.
Service work orders
Use this to create work orders where there is no previously defined structure of items. When the service work order is created it is possible to select any items to be recorded against it.
Service work can be used for recording maintenance time, training time etc.
The items used in a service work order can be invoiced from a customer on completion of the order. This differs from production work orders where the product itself is invoiced.
Entering work hours
There are three ways to enter work hours against a work order: from the work order, from the cell if the work order is routed, or from a work hour view for an individual person.
In the latter case a person can see in one place their total hours for a day and update that information.
There is a time clock system to record operators presence on the job and work hours.
Work queue at a cell
An operator at a cell has a screen showing the work orders queued or active at that cell. Work can be progressed by clicking work orders as “Start”, “Pause” or “Stop”. This data entry can also be made by scanning a barcode on the work order traveller, so that no keyboard or mouse is needed in high transaction factory environments.
When using a subcontractor or a network or subcontractors, the subcontractor can use this simple screen to progress work in the same way as different cells in the same factory.
Materials, time and subcontract usage can also be recorded at the cell.
Time Clock
Operators can be clocked into the factory using the time clock system. This is suitable for use as a kiosk-type of terminal where the terminal is situated at for instance the factory gate.
Production planner (Production in Manu Online)
Production in Manu Online – The production planner allows rescheduling of work orders to suit the rough cut capacity, work or machine time loading and availability of materials. Rescheduling is done by loading the current production situation to a temporary work space, making the necessary changes and then updating these changes back to production.
Using barcodes in production
Barcoding can be used in production and inventory control to simplify data entry. Barcodes are printed on reports or labels using the code 39 barcode font. These are then read by barcode scanners connected to the computers keyboard or USB port. There is no requirement for special software to use barcoding in Manu Online.
Barcodes can exist as commands which are either printed on each work order or statically, or as item ids which can be printed at receipt or statically for instance as shelf labels.
Bar codes are used in five main areas:
- Work flow in production: controlling the flow of work orders from cell to cell using start, pause and complete commands.
- Collecting work hours to work orders: one person can record that he is working on a certain work order; when the next is started the system will record the elapsed time and book the cost to that work order.
- Recording material usage: scan in item and quantity used to maintain inventory control and record material costs to work orders.
- Clock in and clock out: a single code scan can clock in or out a person to the clock card system.
- General data entry: for instance recording serial numbers.
Invoicing
The Invoicing section has support for both sales and purchase invoicing and payments.
Manu Online Enterprise Edition also supports a custom barcode module. This module allows us to customise the code that executes when a certain barcode is scanned. Contact Manu Online support if you are interested in this feature.
Scheduling
Resource scheduling is carried out automatically when sales orders, work orders or purchase orders are entered or changed. The scheduling page of the Production section is for manually rescheduling selected operations. It is used when it is necessary to change the priority of sales orders or to update scheduling information after unusual item activities such as manually changing inventory quantities. Scheduling operates by Business Unit.
Sales order activation
The basic action when an sales order is activated for is to attempt to allocate the quantity of product each line according to the following sequence. If product is partly available at each step, then the remainder continues. If the product is not planned for manufacturing then the sequence goes directly to purchasing.
- Attempt to allocate product from available stock.
- Attempt to allocate from an open work order.
- Plan a work order
- For each item in the product structure, if manufactured, repeat above.
- For purchase items, attempt to allocate item from available stock
- Attempt to allocate from an inbound purchase order
- Plan a purchase order
Work orders
When a work order is created it will propose to allocate to itself any planned work orders that exist. The planned work orders are listed at work order creation time. If the quantity of the work order is greater than all planned, then the excess is available for future allocations from future sales orders or higher level work orders if a subassembly. A work order can be allocated to multiple sales orders, which is typical in a make-to-stock environment.
Dedicated work orders
If a work order is dedicated to a sales order, its allocation cannot be changed and it must be unique to that sales order.
Back to back sales orders
If a sales order is marked as back to back, its lines are allocated to the lines on the linked purchase order. It will ignore items in stock and on other orders.
Through put times
The scheduling system works backwards from the sales order promised date. For work orders the system takes account of the number of working days set per week (default 5) and the number of periods per day. (The length of a period is set in the company settings, typically 1 hour or 1 minute). The work order through put time is set in the item card as the number of periods per unit plus a fixed number of periods.
For purchase orders the planned start date of the purchase order is set on the item card of the purchased material in days. Of course it is possible to buy at any time, but this date is set as the typical maximum delivery time.
Scheduling window
The system has parameters that tell if a new purchase order or work order plan is to be made even if there is an existing order available, but that the available order is coming too late. These date windows are set in the control panel for the scheduling.
The night-run for reallocation
Each night there is a reallocation run that may change the allocations.
The purposes of the night run are:
- Allow for any manual stock corrections made during the day.
- Allow for any manually made “crossed” allocations to be fixed. For instance it is possible to ship product allocated to customer A to customer B. The system will warn of this but not prevent it. The night run will reset the allocations correctly after this event.
- Reschedule materials according to delivery dates
Regarding the last item, the system is designed to reallocate purchased materials according to delivery dates. The logic of this is as follows:
- Planned work orders: The night run allocates the material to planned work orders using sales order promise date as order. The sales order which has earliest promise date, gets the material first. Planned work orders get the material always after open work orders, even though the promise date of planned work order is before the planned start date of open work order.
- Open work orders: The night run allocates the material to open work orders using work order dates as the order. The work order which has earliest planned start date, gets the material first. Material allocation to the open work orders can be managed also by work order priorities. The work order priority can be 1 – 100. Highest priority is 100. The work order, which has the highest priority, gets the material first. If the priority is under 10, the work order gets the material even after planned work orders. If work orders have same priority, the materials are allocated using the work order dates as order.
Get in touch about your production challenges today