Parquet Flooring Manufacturer
Parquet Flooring Manufacturer
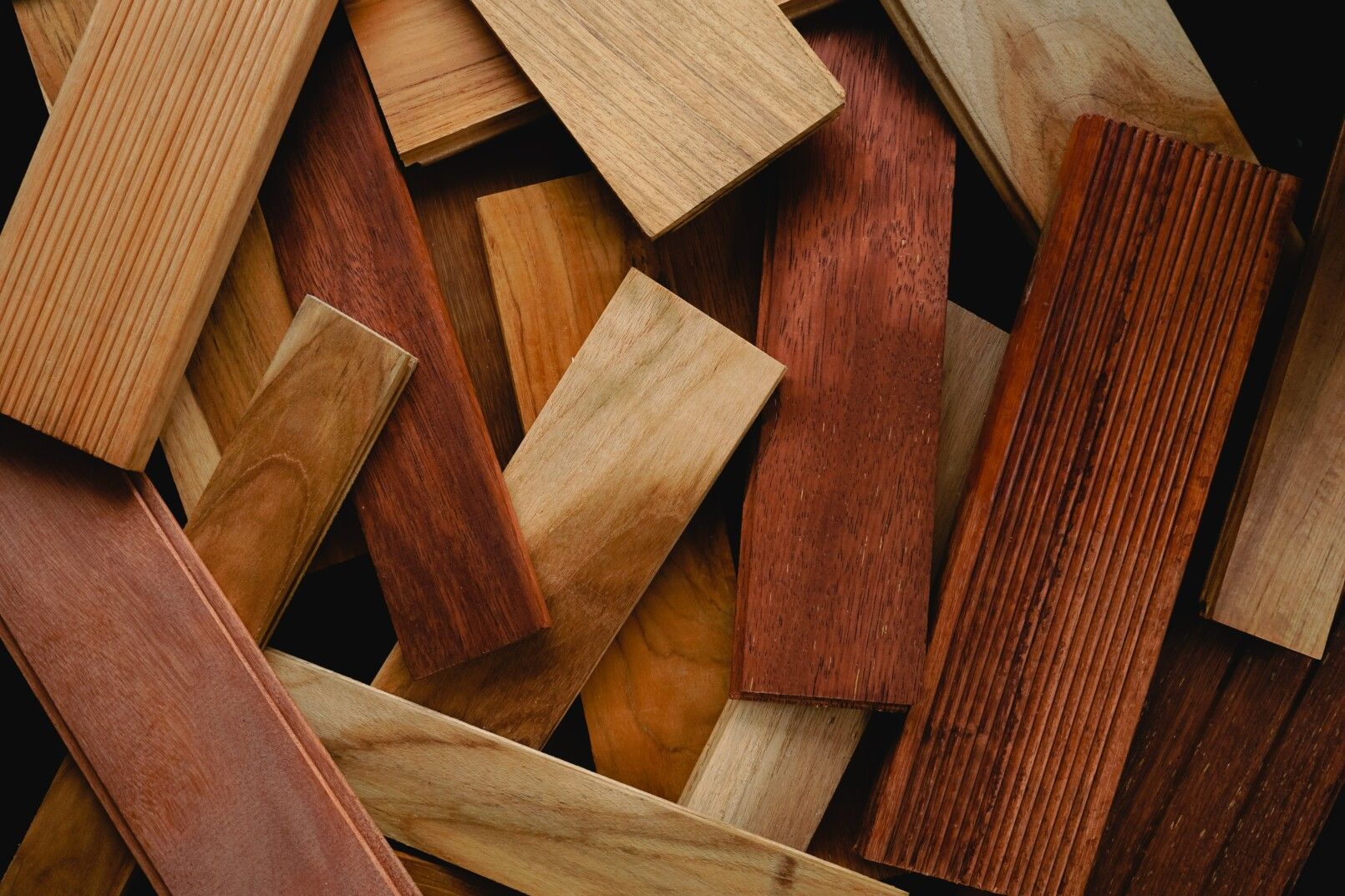
From forest to floor
Parquet floor is manufactured from different grades of timber in a largely automated process line. How does an ERP system help with these business processes?
The raw timber arrives by truck from the forest via the saw mill and first has to be dried in massive low-temperature ovens. This takes several weeks. Of course, the quantities are approximate and measured in cubic meters at this stage. There are several species of wood, including oak, ash, and beech.
The planks are then taken into the factory building and sawn and planed to size. These are stacked in a controlled environment inside the factory while waiting to be turned into flooring. The flooring itself uses the same wood glued either side of a central structure of small wooden strips. By using the same wood on both sides, the natural tendency of the board to warp is eliminated. The wood is graded as it passes through the machine to “better” and “worse” sides so that the best side will later be varnished. After the final machining of the surface, the floor passes to surface finishing, which may be oiling or varnishing. Finally, the boards are shrink-wrapped for final retail packaging.
There is a lot of wood in the factory; it is stacked to the ceilings. There is also a lot of high-speed automated machinery. There are about 50 employees working a two-shift system and only a small management staff.
The challenge for controlling the operation is the combination of long lead time (due to the drying of the wood), the natural variability of the quality (it is never quite certain how much quality product can be obtained from a certain amount of raw timber), and fluctuating customer demand.
Manu Online was used to control the production process of the parquet floor so that at any time it could be clearly seen what materials were where and how they related to current sales orders. At any time, sales order reservations would stretch a certain way back down the production process, but at the beginning of the process, materials were being put in against manager forecasts. To help make these decisions, it was essential that a clear real-time report of stock values (at all stages of production) against sales reservations be available. The situation was complicated by changes in the unit of measure between each stage. Raw wood is purchased in cubic meters, while the final product is in packages with a secondary unit of square meters. In between are boards and square meters.
How the ERP system helped
The item naming and production templates and product families were analysed and set up in a logical way. Each stage of production had its own code. It was not actually needed to create work cells because the stage of production could clearly be identified by the name of the product. The conversions were handled by the different steps in the production and also the case of multiple items being produced by one work order (different grade woods).
Finally, the system was automated by using data collection software in the factory to create the completed work orders. The basic product requirements could be printed from the ERP system and slack capacity was used by starting batches of flooring at the different stages(parquet floor). The data collection system measured the wood going into the machine and the product coming out. When the operator pressed the “complete” button, the data was transferred to the ERP system as an electronic message and a completed work order was created with correct material usage, work hours, and product completed.