How To Reduce Manufacturing Costs [With Examples]
How To Reduce Manufacturing Costs [With Examples]
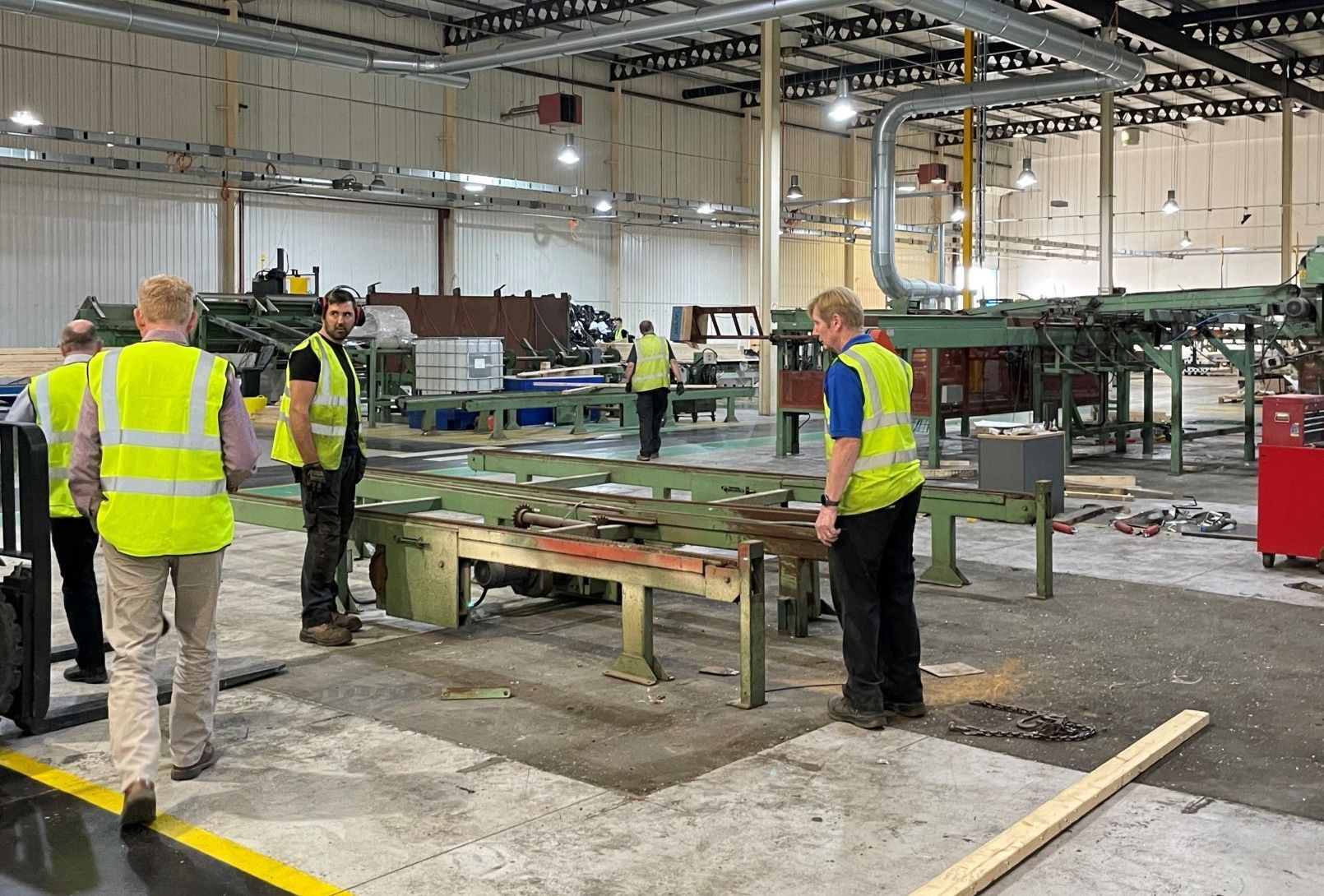
How To Reduce Manufacturing Costs [With Examples]
Whether you produce office supplies or cosmetics, reducing manufacturing costs in any business can be a challenge. But with the right cost reduction strategies, it’s possible to cut expenses, boost profits, and stay on top of your cash flow.
Manufacturing companies typically have many costs associated with their production process.
These can include raw materials, equipment purchases and maintenance, labour costs, facility expenses, taxes, and more. To stay competitive in the market and remain profitable as a business, reducing these costs is essential.
This guide provides an overview of the most effective strategies that manufacturing companies can use to reduce costs and expenses, as well as a brief run through some of the cost challenges you might currently be facing as a manufacturer.
In short the best way to reduce costs is to make your whole operation run faster and leaner. This will keep your manufacturing operations closer to customer demand which helps you beat your competition in the marketplace as well as reducing cost. In reality the only way to run manufacturing operations faster is to have a good manufacturing ERP system implemented.
Challenges to reducing manufacturing costs
If you’re trying to reduce production costs in a manufacturing organization, you’ll know all too well that it’s not an easy task. Whether you’re a CIO, CFO, or production manager, there are several unique challenges you need to face when trying to calculate manufacturing costs – and reduce them.
These may include:
- Rising materials costs: Direct material costs typically account for the majority of manufacturing costs. With the increasing prices of raw material s and continuously fluctuating market trends, it can be difficult to predict material costs accurately.
- Increased labor costs: Direct labor costs tend to be the second-highest cost item in a manufacturing organization. As salaries and wages increase, so too do labor costs, making it difficult to keep them under control.
- Outdated technology or processes: Many organizations are held back by outdated technology, processes, and systems that no longer suit their needs. This can lead to higher overhead costs and an inability to stay competitive.
- Supply chain inefficiencies : As production processes become more complex, so too do the supply chains that feed into them. It’s important to have a grip on your entire supply chain to ensure you not only reduce costs but also improve efficiency and performance.
- Increasing competition: As competition in the manufacturing sector increases, so does the need to reduce costs. In order to stay competitive, it’s essential for manufacturers of all sizes to find ways to lower their production costs and make their business more cost-effective.
It may feel like you’re fighting a losing battle against rising raw material prices, labor costs, and energy expenses. And while these challenges make it difficult to limit overhead, reducing costs doesn’t have to be a losing battle.
These challenges are a very real problem for manufacturing business leaders, but there are other steps you can take to combat these growing costs.
How to reduce manufacturing costs in 8 steps
Here are some proactive steps you can take to reduce your manufacturing costs:
Identify areas of cost reduction
To reduce overhead costs , you need to first identify areas where cost reduction is needed – and where it’s possible. This may include materials, labor, energy costs, and other overhead expenses like those listed above.
Only once you have a clear picture of your manufacturing expenses in mind can you move on to creating your manufacturing cost reduction strategies, so this is the number one step you should take, whatever manufacturing sector you’re in.
Once you have identified areas where you can reduce costs, it’s important to investigate the potential for cost-cutting in each one, which is where the rest of our tips will come in handy.
Utilize ERP systems for cost management
For any manufacturer looking to reduce costs, ERP software can be an essential tool.
Enterprise Resource Planning (ERP) for manufacturers is one of the best ways to reduce costs and increase efficiency. ERP software provides insight into the entire manufacturing process, from production planning to inventory management.
Above that, ERP systems integrate all manufacturing processes into one comprehensive system, making it easier to manage multiple cost elements and accurately track them.
ERP software can then help you identify areas where cost efficiencies can be made and provide easy-to-use tools for monitoring the progress of those efforts.
Streamline processes to reduce waste
Simplifying supply chain management processes can also help you reduce waste and save on those precious and costly raw materials.
When it comes to streamlining manufacturing processes , the goal should be to reduce the number of steps in your process. This will help you save time and money by eliminating unnecessary activities that don’t add value.
Reducing complexity in your manufacturing process can also help you to reduce waste by ensuring that parts and materials are being used efficiently and reducing the risk of errors. With this strategy, you can reduce costs associated with wasted materials and time spent correcting errors.
You can also look into automating certain parts of the manufacturing process (such as machine monitoring or inventory tracking) to minimize manual labor costs, which we’ll look into in a bit more detail shortly!
Leverage technology for improved efficiency
The manufacturing process can be improved with the help of technology. By implementing automated systems for production planning and inventory management, you can reduce labor costs and save time.
Advanced technologies such as 3D printing, Industry 4.0, real-time data and AI-driven analytics can all help to improve efficiency and reduce costs associated with labor and resource waste.
Automation (such as machine monitoring and inventory tracking) can also save you time and money. By allowing machines to run more efficiently, you can reduce the amount of manual labor needed and achieve higher output with fewer resources.
Finally, MRP and ERP systems can help you leverage technology for improve efficiency, providing valuable insights into overall cost savings. With an ERP and MRP system, you can easily track production costs, material prices, inventory levels, and other important data that can help inform your decisions.
If you are having challenges managing your business processes with spreadsheets or a system that is too simple for your operations, you will benefit from the power and scalability of Manu Online.
Invest in automation and robotics to reduce labor costs
As we mentioned, both direct and indirect labor costs can be reduced by investing in automation and robotics.
Robotics and automated systems for production planning, inventory management, and machine monitoring are all essential to reducing labor costs. Robotics can help automate repetitive tasks, reduce human error, and improve the speed of production processes.
Automation is critical for keeping labor costs down in any manufacturing operation, as it allows you to quickly adapt to changing customer needs, reduce waste, and increase efficiency while keeping up with industry-wide digitization pressures.
Automated systems can also free up time that would have been spent manually managing the production process and can reduce the cost of labor.
Adopt a culture of continuous improvement
It’s also important to implement a culture of continuous improvement from the top down in your manufacturing operations.
By making small and incremental changes to the manufacturing process and instilling a sense of ownership within your team, you can create an environment where employees are encouraged to identify cost-saving opportunities and make improvements to the process on their own.
Continuous improvement also allows for quick adaptation to changing customer needs, meaning you can respond quickly to changes in demand and keep up with industry trends.
Use ongoing data analytics to identify further cost savings opportunities
Manufacturing data analytics can help you identify areas where ongoing cost savings may be possible. With data-driven insights, you can quickly pinpoint areas of inefficiency and develop strategies to reduce costs associated with materials, labor, and other production processes.
By analyzing key performance indicators (KPIs) such as time spent on the manufacturing floor, inventory levels, energy consumption, and production costs, you can pinpoint potential savings opportunities. With this information, you can develop strategies to reduce labor costs, optimize resource usage, and increase efficiencies across the manufacturing process.
For example, if you track that your energy consumption is particularly high, your energy costs could be reduced by implementing a more efficient lighting system or installing energy-saving devices.
In addition, data analytics can help you identify any areas of waste and highlight process improvements that need to be made in order to achieve greater cost savings. With this information, you can develop strategies for improving the production process and reducing labor costs.
3 examples of manufacturing cost reduction in action
Angel Forest
Angel Forest automated high-volume and complex business transactions with Manu Online Multi Company Edition.
Angel Forest is a wood products company that imports large volumes of dried timber and processes it for resale to customers according to their requirements. Processing might be so simple as cross-cutting to length or sawing to the right width, or more complex operations such as treatment or packing to prefab home requirements. This is a classic case of “near-shoring” for the final cut of the timber so that exact demand can be met.
Manu Online worked together with Angel Forest to implement a system that provides extensive support for barcoding in manufacturing and yard operations, support for customised processing of their materials in production, connection to PowerBi reporting etc. All the requirements that were needed to make a successful ERP implementation – and keep costs down.
“Our objective was to have a high speed, heavily automated operation so that we could keep our own costs down. This is what we achieved with Manu Online.”
Paul Walker – IT Manager Angel Forest
Ziath
Ziath grew from £250K to £2.5 mil using Manu Online’s Cloud-Based ERP.
Founded in 2005, Ziath develops innovative new products designed to simplify processes in life science organisations, from academia, to the biotech and pharma industries.
With our ERP, Ziath was able to effortlessly track production, materials, and inventory information. This enabled them to reduce inventory costs, speed up their throughput time and increase profits.
Manu Online’s ERP helped Ziath:
Reduce inventory costs, speed up throughput, increase profit:
“We went from 250k and 5 staff to 2.5mil GBP and 30 staff using Manu ERP for the past 10 years.”
Avoid expensive upfront costs :
“We had a look at other ERP solutions but the amount of customisation, the cost per year running and set up was quite large. Plus, some of the others weren’t as focused hardcore on manufacturing so for us they weren’t what we needed. Manu Online’s cost was good.”
Chiller Air Conditioning
The advanced features of Manu Online’s ERP system were critical to the revenue and profit growth of air conditioning manufacturer Chiller.
These features included sales configuration, real-time planning, and messaging integration for improved efficiency, and helped to truly transform the organization – saving valuable time and expenses.
Over the years, Chiller transformed from a low-profit metals fabricator to a high-margin mass customisation producer, and eventually into a full-service provider whose widening share of revenue is generated by after-sales service.
As a result, the company’s revenue and profits multiplied.
This project serves as a powerful reminder of the need to evaluate an ERP system within the context of a company’s overall market strategy.
Closing thoughts
Reducing labour costs is essential for any manufacturing operation – and reduced manufacturing costs are just one of the numerous benefits of a Manufacturing ERP System.
At Manu Online, our ERP and MRP Systems are designed for the manufacturing workforce of the future. Our solutions are designed to help you reduce labor costs, automate processes, and improve efficiency across your production floor and entire supply chain.
If you’re looking for a way to reduce labor costs in your manufacturing operation, contact us today – we’d be happy to discuss the benefits of our ERP and MRP Systems with you!
Reducing manufacturing process costs FAQs
How can manufacturers reduce overhead costs?
Manufacturers can reduce overhead costs by automating production processes, implementing a culture of continuous improvement, and using data analytics to identify further cost savings opportunities. Additionally, manufacturers should consider investing in new technologies such as ERP systems, robotics, and automated systems for inventory management and machine monitoring.
How to reduce cost in lean manufacturing?
Lean manufacturing is a methodology that focuses on eliminating waste and improving efficiency. To reduce costs using lean manufacturing, manufacturers should identify areas of inefficiency and focus on streamlining processes and reducing waste.
Additionally, manufacturers should consider investing in new technology such as automation, robotics, and ERP systems to further increase efficiency and reduce labor costs.
What are the three major costs of manufacturing?
The three major costs of manufacturing are materials, labour, and overhead. Materials include the raw goods necessary for production, while labour refers to the cost of employing workers to manufacture products. Overhead includes other costs associated with running a manufacturing business such as utilities, equipment rental fees, and insurance.