How To Manage an ERP Implementation Project
How To Manage an ERP Implementation Project
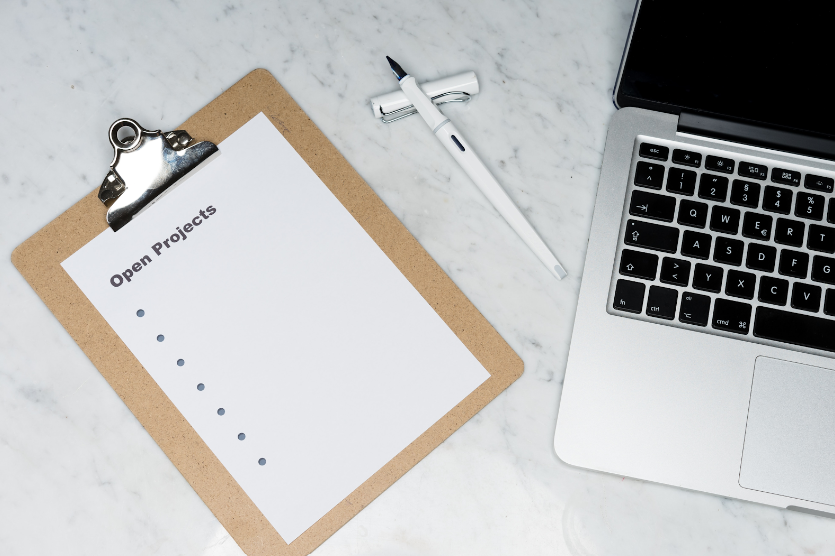
How To Manage an ERP Implementation Project
Managing an ERP implementation project can be a daunting task. It requires careful planning, organisation, and oversight to ensure the successful completion of the project on time and within budget.
Depending on the size of the company and the scope of the project, ERP projects can either be relatively simple or then complex projects that require coordination between many different teams, stakeholders, and potentially even vendors and customers.
Manu Online has been involved in hundreds of implementation projects both large and small. We have divided our guidelines into “ Short form ” and “ Long form ” projects. If in doubt it is better to follow a more formal process even this may feel daunting for a small organisation.
To decide between the two, the key factors are the experience of existing staff with a formal ERP system and the amount of changes that are happening in the organisation’s business practices at the same time as the new system is being implemented. It’s clear that a changeover of an existing ERP to a newer product with trained staff and the same processes is going to be a whole lot easier than if such basic features as part numbering are not yet implemented in the company and no one has used an ERP system before.
In this article, we will discuss how you can effectively manage more complex ERP implementations by outlining each step in the process including scope definition and budgeting, ERP vendor allocation, and employee adoption.
We will also provide tips for ensuring your team stays on track throughout the duration of the project so that you can deliver results with minimal disruption or delays along the way.
Finally, we will explore best practices for measuring success post-implementation so that you can maximise ROI from your investment in new technology solutions. So, let’s dive in!
Enterprise resource planning (ERP) project management basics
First things first. Before you begin, it’s important to understand the basics of ERP implementation and project management. What is it? Why is it worth it? And how can it benefit you ?
Well, managing ERP projects is all about coordinating all your organisation’s stakeholders in order to ensure a successful implementation. This includes monitoring vendor performance and effectively supporting ERP project team members throughout the project.
It also requires effective risk management protocols so as to minimise potential delays or disruptions due to unforeseen circumstances. As such, the management of these projects is critical for their success.
Key responsibilities of an ERP implementation project manager include:
- Defining the scope and budget for the project
- Allocating resources to different departments and vendors
- Managing risk throughout the project lifecycle
- Monitoring the progress of tasks and milestones
- Creating reports and dashboards to track results
- Assisting in employee adoption of new technology or processes
- Ongoing cost management and optimization of operations.
Why should I bother?
Implementing enterprise resource planning (ERP) software not only helps organisations streamline and automate critical business processes, but it also provides valuable insights that help you make smarter decisions about your business.
How does this affect you as a business leader? In short: an ERP system can save time, reduce costs, and increase efficiency. Plus, implementing an ERP system is often a much less expensive option than customising existing processes or investing in new technology solutions.
Ultimately, an ERP system is a long-term investment that can significantly boost performance and profitability for your organisation, saving you a few headaches in the process.
How to manage an ERP implementation project effectively
Identify your specific business needs.
It’s important to start by identifying what specific needs your company has when it comes to an ERP implementation.
Manufacturers in particular have specific requirements and objectives when it comes to their ERP implementation project. For example, manufacturers rely on the ability to manage their inventory, track production costs, and streamline production processes. With a tailored ERP system , these tasks become much easier to accomplish.
In addition, many manufacturers need to monitor customer orders, generate quotes and invoices, and automate billing processes. All of these tasks can be made much simpler with the help of ERP tools.
Key questions to ask at this stage include:
- What business functions and business practices will be impacted? How can you minimize disruption?
- How long will it take to implement the system and become operational? Do you have a deadline for the project?
- What are the desired outcomes? What specific processes and KPIs do you hope to improve with your ERP?
- Who are the key stakeholders that need to be involved with this project? From human resources to finance to operations, consider your entire organisation.
Assess project scope and cost control
The next step in managing an ERP implementation project is to assess the scope of the project and ensure that you have a sound plan for cost control. This means creating a realistic budget and timeline as well as planning ahead for any potential risks or delays.
It also involves assessing how the new ERP system will affect your current financial performance, resource utilisation, and other key metrics. This will help you make sure that the project costs are well-suited to your needs and that it won’t overburden your existing resources.
Key questions to ask at this stage include:
- What is the total estimated cost of the project? Can you fit it into your current resource management?
- How will you manage changes to scope and timeline as the project progresses?
- Are there any risks or potential disruptions that could delay progress in implementing the system?
- Who will be responsible for monitoring progress and providing feedback?
Research different ERP solutions and choose the best fit for your business
Once you have a clear understanding of your project, it’s time to begin researching different ERP vendors and solutions. Evaluate each vendor’s capabilities, customer service record, pricing model, and technology platform. Make sure to ask questions about the vendor’s experience in implementing similar projects for other companies.
You should also find an ERP vendor that provides solutions designed to fit the needs of your workforce and organisation. For example, if you’re a manufacturer, a tailored Manufacturing ERP System will provide the right features for managing your operations.
Features you will need to look out for include:
- Ease of Use
- Customizability
- Traceability
- MRP in Real-time
- Inventory Control
- Integrations
At Manu Online, we provide an ERP system that caters to the unique needs of manufacturers, with features such as inventory control and MRP in real-time. We also offer a wide range of integrations to make sure that our clients get the most out of their ERP projects.
Create a detailed implementation plan with project timelines and milestones
The next step in managing an ERP implementation project is to create a detailed implementation plan.
This plan should include a specific project timeline and milestones to ensure that the project schedule stays on track. It should also set expectations for members of the team, assign tasks and responsibilities, and lay out any contingencies that may arise throughout the project.
Project planning tools like Gantt charts are a great way to visualise and manage project timelines. They allow you to easily identify potential risks or bottlenecks in the project plans and make adjustments before it’s too late.
Some questions to consider while planning your ERP project include:
- What are the main tasks that need to be completed and who will be responsible for each task?
- Are you using an ERP vendor that can handle key implementation processes or do you need to take it in-house?
- What actions need to be taken to take this project from start to finish? When should each task be completed by?
Establish clear communication channels
To ensure everyone is on the same page and fully informed throughout the process, it’s important to communicate the project plan , timeline, and goals clearly to all stakeholders.
This might include creating a dedicated team of ERP project managers who can oversee each part of the project and keep in regular contact with the ERP vendor or other stakeholders.
You should also create clear channels for communication between the ERP project team and anyone else involved in the process, such as supplier partners or customer service personnel. This will help to ensure that your project runs smoothly and efficiently.
Here are some key questions to help you assess and establish clear communication channels:
- Who needs to be involved in the project and who is responsible for overseeing each stage?
- How will each party communicate with one another?
- What processes need to be in place for reporting progress and dealing with project issues or delays?
- What are the protocols for managing changes or requests during the ERP implementation process?
“Prototype” the system properly
The project group must be able to set up and run the system in a “prototyping” environment. Before going live this can be the main account itself. After going live a separate account would be needed with the same configuration as the production account.
Manu Online provides tools for different levels of data deletion while prototyping. This enables the project team to delete sections of data and upload it again (typically from Excel) and then run through the basic business process with perhaps a slightly changed configuration of the system. Deleting and reloading should be possible in a few minutes to make this practical.
During the prototyping stage there may be feature requests from stakeholders. Each request needs to be evaluated is it achievable within the new system “out of the box”, is a new feature or connected app required, or even if there is a much better way of achieving the same result with existing tools in the system.
Document the processes
Produce simple documentation of how the system works in your company’s environment. These documents have two benefits. First is a user guide for new users. Together with the system’s own documentation it shows how the system works here in this organisation . The documentation can also be used as a base for the the company’s quality certifications.
Train employees on how to use the new system effectively
Another part of risk mitigation is the adequate training of employees on how to use the new ERP system. This will help ensure that the transition to the new system is smoother and less disruptive to operations.
Although it seems like an added cost, investing in effective ERP user training will save you all that money in the long run by reducing errors and preventing unnecessary delays or disruption during implementation. Here are some questions to consider when training your employees:
- What kind of ERP system user training is necessary?
- Who will be responsible for conducting the training and ensuring that everyone understands how to use the new system?
- How can users practice using the system before it goes live?
Monitor progress regularly, making adjustments as needed
The final step in managing an ERP project is to monitor progress regularly and adjust accordingly. This means setting up regular meetings with the project team to review progress or using analytics tools to track project performance.
It’s important to identify areas where things are going well and those that need further attention. You should also be prepared to make changes or adjustments to the project plan if needed.
You may also need to assess risks and potential problems in the project plan and create contingency plans for how you’ll respond in case of any delays or issues. Here are some questions to consider when monitoring your ERP project progress:
- What analytics tools can you use to measure project performance?
- What areas are going according to plan and which areas require more attention?
- What actions should be taken to mitigate potential risks or delays?
Post-implementation tips
By following these steps, you can ensure that your ERP implementation project is managed effectively and efficiently. With careful planning, clear communication channels, and regular monitoring of progress, you’ll be better prepared for a successful ERP launch.
Once the new ERP system is up and running, it’s important to ensure that your team continues to use it properly. Here are some final tips for post-implementation success:
- Regularly review business processes and make changes as needed.
- Keep all stakeholders informed of any changes or updates to the system.
- Provide ongoing training and support for users.
- Set up regular reviews of the system to identify areas where it can be improved or optimized.
Closing thoughts
Manu Online’s Manufacturing ERP Solutions stand out from the crowd in that they are designed for the manufacturing workforce and business operations. From scheduling to inventory and analytics, it is the perfect solution for any size manufacturing environment.
We can also help you ensure a successful implementation with project progress and project performance updates to help you manage your ERP implementation project more effectively.
With Manu Online’s Manufacturing ERP Solution, you can rest assured that your project will be managed well from start to finish and that you’ll be able to take advantage of the full power of an ERP system.
Managing ERP software implementation - FAQs
What is an ERP system project manager?
An ERP project manager is an individual who oversees and manages the implementation of an ERP system. This person is responsible for coordinating all aspects of the project, from planning to testing to user training. ERP project managers must have both technical and managerial skills.
How do I calculate how much an ERP project costs?
The cost of an ERP project depends on the size and complexity of the system being implemented. Our experienced professionals can help you calculate the cost of your project and develop a budget plan that suits your needs.